Despite tremendous progress, there is still much work to do.
Four years after the Produce Traceability Initiative (PTI) target date set by the Produce Marketing Association, United Fresh Produce Association, Canadian Produce Marketing Association and other industry leaders, the industry is still not close to 100 percent compliance when it comes to universal case labeling.
Tremendous progress has been made toward the lofty goal of being able to quickly trace contaminated produce back to its field of origin, but there is still work to be done in meeting this challenge.
“We are not at 100 percent compliance with PTI, and I expect it will be quite a while before we even get close to 100 percent,” says Charles Waud, president of WaudWare in Brampton, Ontario. “In my view, the move to PTI is somewhat stalled right now.”
On the whole, most major grower-shippers are putting traceability labels on their cases, but many smaller farmers are not.
“Certain small farms are complying, but like the rest of the industry, some are also waiting to see what is actually required of them before doing anything,” says Waud.
Even if the pace is glacial, the produce industry is moving toward the goal of being able, in cases of food safety problems, to track produce back to harvest from a particular field on a certain day.
“In some respects, it’s better today than it was when people started talking about it,” says Steve Dean, owner of ProWare Services in Plant City, FL. “I don’t think we’re close to 100 percent, and I don’t think we ever will be unless it’s mandated. People aren’t going to do something they don’t have to do.”
We may be some distance from the goal of universal compliance but enough shippers are already using the PTI label to appreciate the benefits, and to see where the technology must be improved.
Information Please
The next step in advancing the PTI will be developing a system that lets everyone in the supply chain access not just the label, but also the information it signifies.
“There are many companies today that are labeling their product; it’s at least 50 percent of the industry,” says Ray Connelly, vice president of traceability and merchandising at iTradeNetwork in Dublin, CA. “Some retailers and foodservice organizations are starting to request that data be shared via the Advanced Ship Notice (ASN), but we have a ways to go. There is a technical component, but it is more accurate and timelier with an ASN.
“Most of the supermarket and foodservice companies are not requiring the data yet. Wal-Mart and Whole Foods Market are two retailers that have requested a label on every case,” says Connelly.
Without access to the data, produce retailers would still have to make phone calls to track down the field where contaminated produce was harvested.
In order to share the information, the industry needs a universally accepted way of transmitting, storing and accessing it.
“When there is a recall, you want to provide the USDA all the information necessary, quickly, and move on. This will lower the risk to your company of further scrutiny. You want the USDA to see how organized you are.”
— Dave Donat, Produce Pro
“We need to be able to transmit the data electronically,” says Connelly. “Some companies are already working on it. I know Associated Wholesale Grocers is working on it. I know Wal-Mart is taking steps in that direction too.”
This second generation PTI will require a cloud-based system used by everyone in the supply chain.
“It has to move more toward technology taking it over a little bit,” says Dean. “There is not a cloud for everyone to publish information to, and everyone to retrieve it from. Just putting a code on the case doesn’t tell you anything. You would basically have to call the shipper to find out what the label meant in terms of which field the produce came from on what day.”
Another element to consider: there could be side effects from such a cloud-based system, — not the least of which could be giving the consumer access to previously unheard of information through their smartphones as they stroll through the produce department.
“The next step to me has always been to be really transparent to the consumer,” says Charles Shafae, president of dProduce Man in Half Moon Bay, CA. “I would like to be able to have a G-10 number on the produce, so the consumer could go to the website and really see where it is from.
(G-10 is a 10-digit number used internationally, and each digit tells you information about the location.)
“You can not only take it back to the field, you can take it back to the picker of that particular item,” says Shafae.
But the greatest advantage from sharing the information will be the ability to move with great speed and accuracy in the event of a food safety problem.
“It is one thing to track all of this information,” says Dave Donat, president of Produce Pro in Woodridge, IL. “It is quite another to be able to quickly generate this information on demand. When there is a recall, you want to provide the USDA all the information necessary, quickly, and move on. This will lower the risk to your company of further scrutiny. You want the USDA to see how organized you are.
Tying Up Loose Ends
As much progress as the produce industry made in a short time in adopting traceability labels, there are still loose ends, and some of them will be difficult to tie up.
While many customers of the small farmers not using case labels already know where their produce originated, there are situations where produce enters the mainstream and is difficult, if not impossible, to trace.
“Once it’s put in a box and shipped to retailers, they could trace it back to the lot,” says Ron Myers, executive vice president of LinkFresh in Ventura, CA. “But they mix batches or lots, and then put a label on that lot. All of the larger packers are using traceability programs. My opinion, based on what I see, once produce is in cases it could be traced back. They’re putting labels on the cases. The problem is there are mixed lots in those cases, so if there is a recall, we could go overboard and recall more product than actually necessary.”
Traceability becomes even more complex when a truck is rolling down the road loaded with pallets of tomatoes, and each pallet contains more than one lot.
“Each one of the companies that handles the product needs to be able to receive and send the data,” says Connelly. “If I receive a truck with 22 pallets of tomatoes, but those pallets come from 45 different lots, it explodes the complexity of the data.”
The data becomes staggering once you try to track produce that has been cut and washed back to a particular field.
“A lot of companies do value-added,” says John Carpenter, president of Silver Creek Software in Boise, ID. “They’ll take cases and process it. Following that is difficult. The Produce Traceability Initiative was supposed to go from the farm to the fork.”
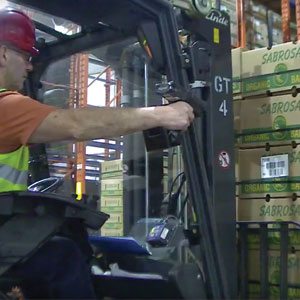
Compliance with universal traceability standards will only approach 100 percent as shippers feel greater pressure to adopt them.
As partners in the U.S. produce supply chain work to tie up loose ends, there is also work to be done bringing imported produce up to the traceability standards already established in the U.S.
“What we can hope for is better relations with international farmers,” says Myers. “What I have seen is there is more of a problem tracing back to a particular farm or field location on produce imported from Mexico, Chile or Australia. They do know what lot the produce came from, but the lot could be one field to 100, depending on the commodity and operation.”
The list of undone work may be daunting, but the produce industry is making undeniable progress on a project essential to improving safety and efficiency.
“We need traceability,” says Carpenter. “It’s taken longer than we expected, and [the process] is expensive, but we definitely need it.”
Then there is the question of small farmers who may never adopt labels, because their produce never travels far from home.
“Small farms are generally not complying; we don’t see evidence of it,” says Donat.
Many small farmers do not feel pressure to adopt PTI, because they are selling directly to the consumers.
“The only area we don’t see traceability is the small direct-to-customers at farmers markets, CSAs, or to restaurants,” says LinkFresh’s Myers. “We’re now focusing on the bottom 20 percent; it’s getting down to the last bit. The industry has done a pretty good job.”
Cost Is King
Among shippers who do enter the mainstream, many will be more likely to adopt PTI as the cost goes down and it becomes more practical and beneficial in numerous ways.
“The real reason for moving slow is the cost,” says Shafae. “As the cost of the technology comes down, more people will convert.”
Associated with lower cost will be integration with newer computer devices, and the younger workers who grew up with them.
“The other thing is the devices,” says Shafae. “As more devices are being used for traceability and other data, more people will use it because the information is easier to get to. Sales of PCs and laptops are decreasing, while sales of smartphones and other mobile devices are increasing. It is easier for the younger employees to use the technology. We are increasing the use of traceability; we are moving faster.”
Tech firms are already making progress in developing more economical traceability systems.
“The cost has already come down around 25 percent from a couple years ago,” says Carpenter. “The cost of going to a lotted system is holding some smaller companies back. Getting barcodes on some kinds of packages is a problem for some people. From where I’m sitting, we’re still at around 60 percent participation in PTI.”
An important part of improving the bottomline will be developing the other business benefits of produce tracking — not the least of which will be improved inventory control.
“I think that the next step, or perhaps a step to take in conjunction with implementing traceability, would be to ensure you can get other business benefits out of its implementation,” says Waud.
“For example, if you implement traceability in conjunction with inventory transactions (like how our solution is designed) then by having more accurate inventory quantities and sales data, you can make better business decisions, reduce mistakes and overselling, etc. This helps you cost justify the implementation of traceability,” explains Waud.
This part of the process will involve tech firms developing better products that are more economical, easier to use, and provide more business benefits, explains Waud.
“I think that for those of us involved in traceability in the produce industry, we will continue to be very busy in the coming years helping our customers implement solutions,” says Waud.
Pressure To Comply
Compliance with universal traceability standards will only approach 100 percent as shippers feel greater pressure to adopt them, and some companies are waiting to learn what regulators tell them they must do.
“Many produce companies are waiting to see what happens with the Food Safety Modernization Act in the USA and the Safe Food for Canadians Act in Canada,” says Waud. “If this legislation is clearly seen to be aligned with PTI, then I expect to see PTI start getting adopted more. However, if there is no clear alignment, then we will continue to see different approaches to traceability being adopted.”
Retailers have, so far, played the greatest role in letting suppliers know what they must do in the area of traceability as part of the cost of doing business.
“It is hard to say if we will ever be at 100 percent,” says Donat. “Most suppliers we see are complying with specific customer demands, as opposed to meeting industry-accepted deadlines. So as usual, our customers’ customers will dictate whether this takes off.”
Many major retailers already require the PTI label, and the future depends on how many other supermarkets join them.
“Uneven demand from the customer base is holding the industry back,” says Donat. “Suppliers see it as a cost burden, and only undertake it when their customers tell them they must.”
There is a trickle down effect already in motion, as some major shippers are already requiring that growers who supply them buy into traceability.
“The big brand names, like Taylor Farms or Dole, have grower relations people working with their growers so they can trace back to the original grower and farm or field location,” says Myers. “Our customers can trace produce back to areas within the field. We can get right back to geo spots within the field.”
But while the PTI remains a work in progress, the project is already having an impact creating a culture change among produce shippers.
“I think people take a little more care before shipping things, because of the transparency,” says Shafae.